Tips for Ensuring a Successful Year-End Inventory Count
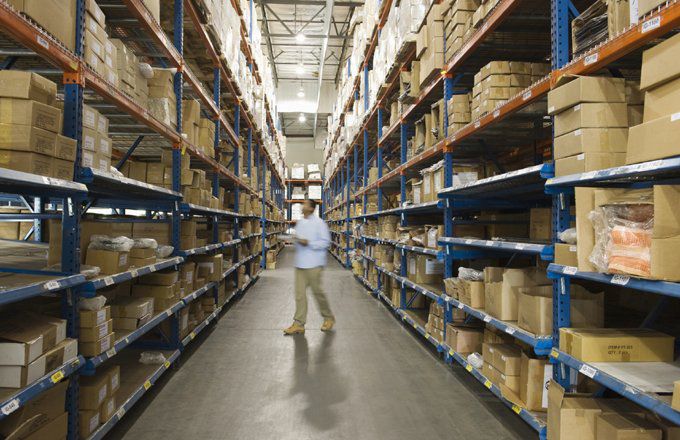
For many people, the end of each year brings with it a time for family and friends, holiday celebrations and hopefully a chance to take some unused vacation days. Unfortunately, this can also be one of the most challenging times of year for businesses, as the period just before the start of the New Year frequently requires completion of physical inventory counts.
Successful inventory counts and the updating of accounting records is paramount in accurate financial reporting. Not only does a company’s inventory balance often serve as collateral for borrowing, the results of an inventory observation could have a material impact on the financial statements, particularly if obsolete or damaged items are identified, or if quantities from the observation do not agree with inventory records.
As auditors, we routinely observe and perform test counts on year-end inventory for our audit clients, and have noted several ways these counts can be improved from both an accuracy and efficiency perspective.
Following are some tips and recommendations for ensuring that your inventory procedures go smoothly and that headaches are avoided after the New Year.
Instructions
Inventory instructions can serve as a strong foundation for count procedures. Employees at different levels within an organization may be involved with performing inventory counts at year-end. Given the complexity that inventory procedures can entail, getting those involved on-board and familiar with the process well in advance goes a long way towards ensuring that inventory is accounted for timely and accurately. Including the following items in the inventory instructions may be beneficial:
- Time and location the inventory will be taking place
- The individual responsible for each area and overall completion of the counts
- When, if any, stops in production and/or shipping and receiving will occur
- Any specific unit of measure considerations
- Any work in process items that employees should be aware of
- How and when internal reconciliation procedures will be handled
- A layout of the area/areas to be counted
Variance analysis
Comparing inventory counts to a benchmark is one approach that a company can utilize to ensure accurate results. Even when inventory is counted (and perhaps re-counted), having a benchmark number to compare the counts to is a good way to determine whether additional procedures should be performed before the count numbers can be relied upon. A company may have a reliable periodic system, whereby the year-end counts can be compared to the system at that point in time. It may be beneficial to establish thresholds (for instance, plus or minus 5% of the system number) to indicate whether or not items need to be flagged for follow-up after they are counted. Blindly updating the inventory records after one count can make them more susceptible to human error. Variance analysis can identify items that were not counted properly or perhaps not counted at all.
Tracking system
Effectively tracking inventory items is a vital aspect of the inventory count process. Two of the most common methods involve inventory tags and inventory count sheets. Typically, tags and count sheets include a full identification of each item. Inventory tags are numbered sequentially and any unneeded tags are appropriately voided. Count sheets contain a list of all items that need to be counted. Having tags, count sheets, or another way of identifying inventory on hand will aid in ensuring all items are counted and reconciled appropriately.
Damaged, obsolete, bill and hold and inventory on consignment
It is important to remember that just because an item is physically on hand, it does not necessarily belong to the company or have value. The year-end inventory count process provides another opportunity for companies to identify any damaged or obsolete inventory, and determine whether or not those items have been appropriately reserved for or written off entirely.
Similarly, companies should be aware of any bill and hold or consignment arrangements whereby the items on hand are actually owned by another party. These items should be appropriately segregated and accounted for. Items that technically are the property of the company but at another location, or any items in transit, should be properly identified and accounted for at year-end.
Cycle counts
Companies with effective and reliable inventory systems may not perform an annual wall-to-wall physical inventory but instead preform cycle counts. Cycle counts involve counting small portions of inventory throughout the year. Many companies will segregate their inventory into high, moderate, and slow moving items, counting portions of high moving items more frequently, moderate moving items less frequently, and slow moving items perhaps only annually.
Performing cycle counts allows management to identify potential errors at a point in time, rather than only at year-end. Doing so often makes the year-end physical count much easier, and gives employees familiarity throughout the year with how procedures need to be performed and errors evaluated, reconciled, and updated.
Supervision
A strong inventory count process can involve many resources, employees and locations, making adequate supervision a must. Having one or two designated employees as a point person(s) for the entire process gives all involved a resource to go to in the event of any errors. Placing an individual in charge who understands the count process, the items being counted, and the variance analysis review, and who has the ability to track and ensure all items are accounted for appropriately, leads to a more efficient and effective process, and holds all team members accountable.
Depending on the size and number of items being counted, a company may want to designate specific individuals to perform re-counts of certain items or all items during the process. This second set of eyes is helpful in identifying any counting errors that variance analysis may not pick up. In addition, if internal resources are not adequate, the company may find it useful to hire an outside firm to perform count procedures for them during the year, at year-end, or both.
Know what you are counting
As simple as it sounds, sometimes items and units of measure can be easily confused. Certain goods may have very similar identifiers and be incorrectly recorded in the inventory records. In addition, inventory may have a specific unit of measure that needs to be followed (square feet or pounds, for example) that is unique to the item or particular product line. Having a team performing counts that is familiar with both the items on hand and the appropriate unit of measure is another way to make sure all items are counted appropriately.
Limit movement, production shipping and receiving
Limiting movement of inventory during the count process is crucial to ensuring items are properly counted and proper cutoff is achieved. A high volume of shipping and receiving or work in process during counts can make it difficult to identify errors, obtain the correct counts, or properly identify cutoff of items sold.
Conclusion
This is by no means an exhaustive list of all areas where inventory counts can be improved. However, auditors observing year-end test counts will be looking for proper cutoff, correct quantities, and completeness of counts as well as indications of obsolete or damaged items. Incorporating some or all of the procedures listed above can go a long way toward streamlining your inventory count process, reporting accurate numbers, and having less headaches with your year-end audits.
If you have any questions about this deduction, please contact Jason Emery or your BNN professional at 800.244.7444.
Disclaimer of Liability: This publication is intended to provide general information to our clients and friends. It does not constitute accounting, tax, investment, or legal advice; nor is it intended to convey a thorough treatment of the subject matter.